What are quality engineering services?
Quality Engineering Services are a set of processes, methodologies, and techniques designed to ensure that a product or service meets the quality standards and the requirements of the stakeholders. In software development, it is the management, development, maintenance, and operation of IT systems. This includes enterprise architectures with a high-quality standard. Quality engineering services typically cover the entire product development cycle, from requirements gathering to post-release maintenance. The focus is on detecting and preventing defects and errors that could affect the performance or usability of the product.
Why we need it?
With quality engineering services, you can validate the product in a timely manner and release it at the earliest. This will help to improve the Quality and reduce the Cost. The product makes it way to the market faster. So, over time, you will receive customer feedback. It will help you solve problems and/or add new features. This will ensure customer satisfaction and the product will stay on the market longer.
The following are some of the key activities that quality engineering services may cover:
1. Quality Assurance (QA)
Quality Assurance is any systematic process of validating the product or service meets the specified requirements and quality standards.
QA establishes and maintains set requirements for developing or manufacturing reliable products. A quality assurance system increases customer confidence and a company’s credibility, while also improving work processes and efficiency, and it enables organization to better compete with others.
2. Quality control (QC)
Quality control (QC) is a process through which a business seeks to ensure that product quality is maintained or improved. QC involves testing products and determining if they are within the specifications for the final product.
3. Quality improvement
This involves identifying areas for improvement in the product or service and implementing changes to improve its quality. It involves establishing a plan for improvement, implementing the plan, and then measuring and evaluating the results to ensure that the desired improvements have been achieved.
Quality improvement is a continuous process, and we can apply to any type of organization. The goal is to increase customer satisfaction, reduce errors and waste, and improve efficiency and effectiveness.
Some common tools used in quality improvement include statistical process control, root cause analysis, Six Sigma, Lean, and Total Quality Management. These tools help organizations identify the root causes of problems and make data-driven decisions to improve those.
4. Process improvement
This involves analyzing the processes used to design, develop, and deliver the product or service, and identifying ways to improve those processes. This helps to make the process more efficient, effective, and valuable. This can involve reducing costs, improving quality, increasing throughput, or enhancing customer satisfaction.
There are many methodologies and tools for process improvement. For example, Lean, Six Sigma, Kaizen, Value Stream Mapping, and Process Mapping. These methodologies help organizations to identify waste, reduce variability, and optimize processes. Certainly, this will help to improve customer satisfaction, reduce costs, and increase efficiency.
5. Risk management
Risk management is an essential aspect of quality engineering as it helps to identify, assess, and mitigate potential risks that may impact the quality of the product or service. In the context of quality engineering, risk management can help identify potential defects in products or processes, and address those before they become serious problems.
One common approach to risk management in quality engineering is the use of Failure Mode and Effects Analysis (FMEA). FMEA involves analyzing the potential failure modes of a product or process, identifying the potential effects of those failures, and developing strategies to prevent or mitigate those failures.
Another important aspect of risk management in quality engineering is the use of statistical process control (SPC). SPC involves monitoring and controlling the performance of a process using statistical methods, which can help identify potential problems before they become serious issues.
6. Compliance management
Compliance management refers to the process of ensuring that a product or service meets the regulatory and legal requirements of the industry it belongs to. It involves identifying applicable laws, regulations, and standards and making sure that the organization complies with them.
Compliance management is an essential aspect of quality engineering as it helps to ensure that the product or service is safe, reliable, and of high quality. Failure to comply with regulations can result in legal and financial consequences, damage to the company’s reputation, and harm to consumers.
Conclusion
Overall, quality engineering services are essential to ensure that a product or service meets the needs and expectations of users and stakeholders, while providing a high level of quality and reliability. With the effective use of various quality engineering methods and tools, you can address Voice Of the Customer (VOC). So, this will be helpful during the processes of product conception, design, development and implementation. Ultimately, the benefits will be visible in the quality level of your organization’s products and services without a doubt.
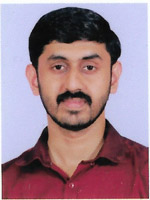
Lead QA Engineer at CeeGees Software Solutions Pvt. Ltd.