We built this for one of Singapore’s largest e-commerce portals.
Non easy dispatch work flows or poor Inventory management system can cause number of challenges and inefficiencies to Businesses. It can hurt their bottom line and customer satisfaction.
Below are some potential flaws that can have negative impact:
- Lack of real time visibility: Without tracking shipments and delivery vehicles in real time, businesses may struggle to keep track of their inventory and provide accurate delivery estimates to customers. This can lead to missed dead lines and customer dissatisfaction.
- Inefficient routing: Businesses may struggle to find the most efficient routes for their delivery vehicles without automate routing. As a result it causes longer delivery times, increased fuel costs, and reduced profitability.
- Poor inventory management: Without an automation system to help manage inventory levels, it is difficult to keep track of their stock levels and may risk running out of popular items.
So there is a greater need of cutting edge logistics technology. An innovative app can help businesses better manage their inventory and ensure faster, more efficient deliveries.
Here is the Challenge
The challenge was to develop a mobile application to help the operations improve the dispatch work flows related with different retail shops and manage the online orders of NTUC and enable different work flows for different order types.
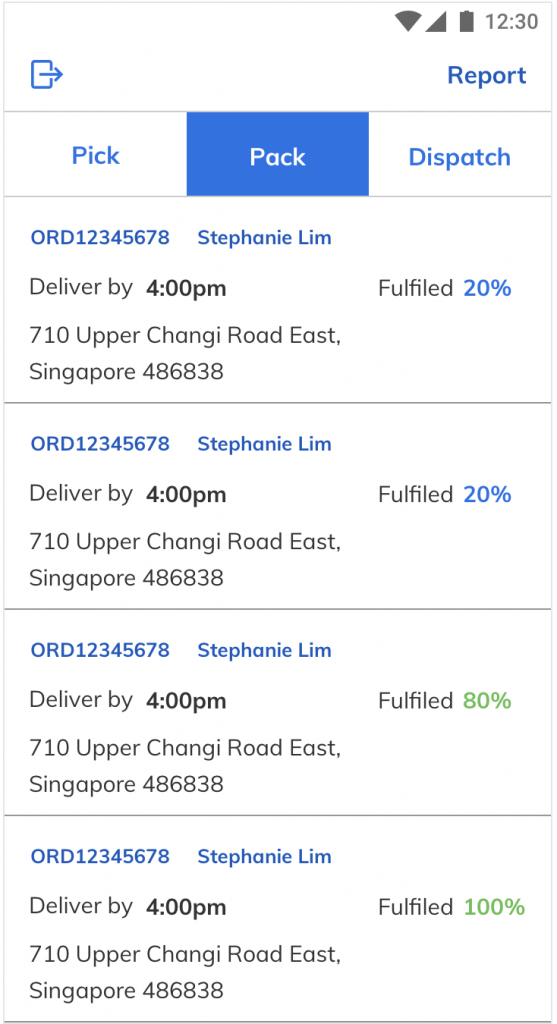
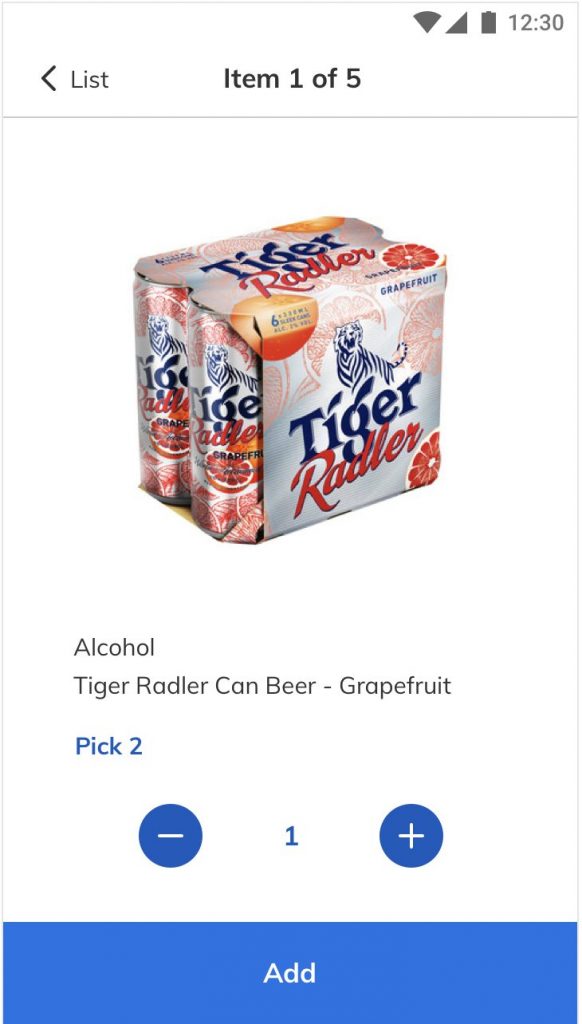
Ceegees was successful to help the client to improve their dispatch operations and deliver exceptional customer experiences. We as a technical team was happy to contribute to their growth and success.
How we helped
We provided a robust system to handle real time transactions and inventory management along with batching multiple orders on delivery routes and vehicles to reduce overall delivery time.
We integrated with existing legacy systems, pulling data efficiently and presenting it in a smart way to enable faster decision making and improve the customer experience.
As a result, the system improved the dispatch time by 34 mins providing a 160% improvement.
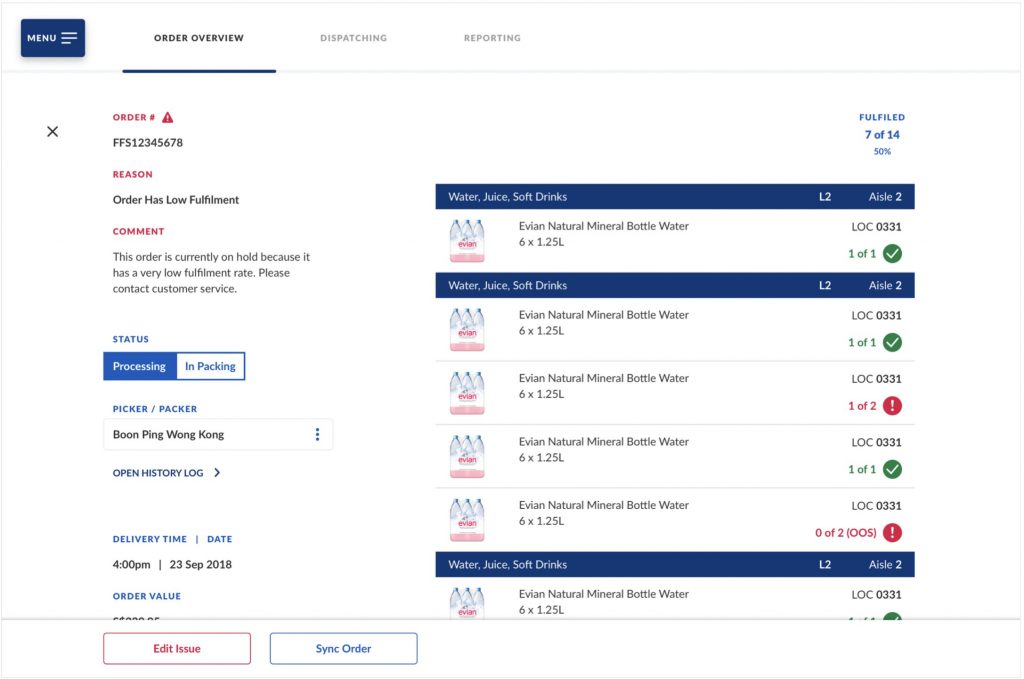
How does the system manage flows
The pick, pack, and dispatch process is an essential part of inventory management in any organization that deals with physical products. This process involves the following steps:
- Receiving an Order: The pick, pack, and dispatch process begins when an order is received from a customer. The order may come through various channels, such as an e-commerce portal, email, phone, or in-person.
- Picking: Once an order is received, the next step is to pick the products from the inventory. This involves locating the products in the warehouse or storage area and collecting the required quantity. The picking process can be done with the help of our app (Pick tab) using barcode scanners or by manual entry.
- Packing: After the products are picked, orders from Pack tab need to be packed. The packing process must ensure that the products are well protected during transportation.
- Labeling: The next step is to label the packages with the customer’s address, order details, and any other relevant information. This information ensures that the package is delivered to the correct customer and location.
- Dispatching: Once the packages are labeled, they are ready for dispatch. Dispatching involves preparing the packages for shipment, which may include sorting packages by destination and selecting the appropriate shipping carrier. The packages are then handed over to the shipping carrier for delivery.
- Updating Inventory: Finally, the inventory system needs to be updated to reflect the products that have been shipped. This ensures that the inventory levels are accurate and up-to-date.
So, the pick, pack, and dispatch process with our automated system ensured that orders are fulfilled accurately and efficiently, leading to satisfied customers and effective inventory management.
Lead Engineer at Ceegees Software Solutions Pvt Ltd
it could be better if add more details of implimentations. Eg: like how the orders grouped based on delivery location to reduce delivery time(any algorithms if used or methods ).